Étude de soudage (Soudage de EN AW-6082-T6 ou 7020-T6 en épaisseur ~ 12 mm)
Cet article technique rédigé par Gérard LIGNIER est une étude fouillée de différents documents du soudage des alliages d'aluminium 6062 T6 et 7020 T6
Il aborde les données opératoires, les données métallurgiques des métaux de base et des métaux d'apport.
1 - Données opératoires :
(les paramètres de soudage sont écrits en rouge, les références bibliographiques en vert et les interrogations restantes en bleu)
Les pièces seront soudées en soudage MIG (le soudage TIG - « Tungsten Inert Gaz » - recommandé pour des soudures de haute qualité - aéronautique - devient problématique dans ces épaisseurs, il n'est guère utilisé, dans la pratique, au-delà de 6 mm d'épaisseur). Le MIG offre quelques avantages intéressants par rapport au TIG :
- Possibilité de vitesse de soudage beaucoup plus élevée ;
- Taux de dépôt de métal d'apport beaucoup plus élevé ;
- Épaisseurs soudables plus importantes (soudage multipasses effectué sans difficultés particulières) ;
- Automatisation relativement facile...
Pour le 6082, il est recommandé un courant continu (contrairement au soudage TIG où il est, sauf applications particulières, alternatif...) pulsé (fil électrode au +, pièce au -, afin que le flux d'électrons, se déplaçant de la pièce vers le fil, casse la couche d'Al[SUB]2[/SUB]O[SUB]3[/SUB] - qui a une T°C[SUB]fusion[/SUB] élevée de ~ 2000°C. De plus, le courant pulsé facilite l'obtention d'un mode de transfert en « spray-arc » (voir T.Ingénieur « BM7732_Soudage MIG-MAG pulsés.pdf », §3 p.2), et voir ci-dessous).
Deux modes de transferts, seulement, sont ici possibles (en effet, le transfert d'arc par court-circuit ne peut pas être obtenu avec des gaz inertes, mais j'avoue ne pas avoir trouvé pourquoi ?) :
- Un transfert du fil par grosses gouttes (dit « globulaire ») impliquant une tension U de soudage moyenne (~ 20 V) et une intensité I également moyenne (~ 150 à 200 A en ~ 12 mm d'épaisseur) ;
- Un transfert du fil par pulvérisation axiale (dit « spray-arc ») impliquant une tension U de soudage haute (20 à 40 V) et une intensité I élevée (~ 280 A en ~ 12 mm d'épaisseur) assurant un fort taux de dépôt en métal d'apport.
Le mode « spray-arc » sera préféré car il permet de délivrer une puissance spécifique élevée P (P = U x I, exprimée en W/cm[SUP]2[/SUP]), absolument nécessaire compte tenu de la capacité calorifique élevée de l'aluminium (conductivité thermique élevée, associée, ici, à une épaisseur non négligeable de 12 mm).
En d'autres termes, l'apport de chaleur doit être rapide et important afin de provoquer une mise en fusion rapide du joint, laquelle a pour but d'annihiler la tendance à la prompte dissipation de cette même chaleur dans la pièce (capacité calorifique élevée = dissipation rapide des calories dans l'assemblage de pièces).
Noter qu'il faudra veiller à travailler, malgré le mode « spray-arc », avec un arc le plus court possible afin d'éviter au maximum les soufflures, surtout avec la série 7xxx sans Cu, type 7020, à cause de la vaporisation du Zn...
De plus, la nécessité (car il y a des usinages après soudage...) de limiter les déformations (si pas de bridage pendant le soudage) ou les contraintes internes (si bridage pendant le soudage), implique d'opérer avec une vitesse de soudage élevée afin d'apporter le minimum d'énergie calorifique W à l'assemblage (W = U x I x t, que l'on peut exprimer en J ou J/cm[SUP]2[/SUP] si l'on parle d'énergie spécifique).
Noter que la diminution de W permettra corollairement de diminuer la création des soufflures en limitant au maximum les phénomènes de vaporisation (le Zn dans le 7020 par exemple) et, permettra, cerise sur le gâteau, d'obtenir un cordon très lisse de bel aspect. Nous verrons une 3[SUP]ème[/SUP] raison à cette limitation au § 2.
On peut résumer tout cela en disant qu'il faudra « frapper fort et vite » en termes de chaleur apportée et avoir un taux de dépôt important, tout en s'efforçant de souder le plus loin possible des usinages ultérieurs ou, pour le moins, de souder symétriquement par rapport à ces usinages pour limiter les effets néfastes des contraintes et/ou déformations générées par le soudage, contraintes et/ou déformations inévitables en soi...
Concernant la protection gazeuse, on préfèrera un mélange Argon + Hélium (type ARCAL 33 d'Air Liquide = 70% Ar + 30% He) à de l'Argon pur (gaz inertes => seulement 2 modes de transferts possibles : pourquoi ?...). L'ajout d'hélium - qui se fait au détriment du prix - permet d'élever la T°C de l'arc et, en cela, permet d'augmenter la vitesse de soudage (=> diminution de t => diminution de W..., voir ci-dessus)...
Pour le 7020, la présence du Zn qui vaporise (T°C[SUB]fusion[/SUB] ~ 420°C, T°C[SUB]ébullition[/SUB] ~ 910°C) et a tendance à souffler l'arc, augmente la propension de l'alliage à générer des soufflures dans le cordon. Afin de les limiter, les recommandations (voir article « Soudage TIG et MIG de l'Aluminium et ses alliages_Pratique du soudage.doc », §19) sont les suivantes :
- Apporter un soin particulier à la préparation des bords à souder ;
- Veiller au bon état de surface du fil d'apport ;
- Sécher, gratter mécaniquement et dégraisser les pièces à assembler ;
- Chercher, malgré le mode de transfert (« spray-arc »), à avoir l'arc le plus court possible.
Nous aborderons au § 3 les nuances des métaux d'apports à apporter, en fonction des alliages à souder.
2 - Données métallurgiques sur le métal de base :
Il faut savoir que les alliages d'aluminium des séries 6xxx (Al-Mg-Si) et 7xxx (Al-Zn-Mg avec ou sans Cu) sont des alliages à traitement thermique encore dits « à durcissement structural ».
Appelés ainsi car ils ont la particularité de ne pas durcir immédiatement après leur trempe. Ils sont, en effet, encore facilement déformables aussitôt après (la trempe) (le type de trempe dépendra de l'alliage, eau pour Al-Cu, air pour Al-Zn, voir article « Aluminiums_Durcissement par précipitation.pdf », §2.2 p.2), ce qui permet de les industrialiser - par formage, pliage, matriçage,... - sans difficultés pendant un certain laps de temps. Ils ne durcissent que progressivement après la trempe, selon un temps plus ou moins long (à titre indicatif ~ 1 mois si ce durcissement, appelé « vieillissement », se fait à T°C[SUB]ambiante[/SUB]).
Juste après la trempe (et après la génération d'un équilibre métastable comme dans toute trempe), des regroupements d'atomes des éléments d'alliages présents (Al + Mg, Si, Zn,...) - vus comme en excès par la matrice - sont initiés au sein de la matrice (on parle de « germes » ou zones de Guinier-Preston ; il n'y a pas encore de phénomène de « démixtion » = pas de séparation (non miscibilité) des phases en présence). Ces regroupements sont, la plupart du temps, très limités en nombre d'atomes.
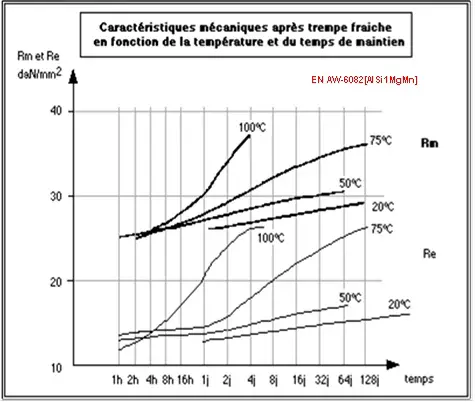
On parle de vieillissement naturel lorsque ce durcissement s'effectue à la T°C[SUB]ambiante[/SUB] . Ce vieillissement est appelé « maturation » (il est plutôt long - voir courbes jointes ci-dessus et ci-dessous) et l'alliage est alors dit « trempé - mûri », c'est l'état métallurgique T4. Seuls les alliages des séries 2xxx, 6xxx et 7xxx ainsi que certains alliages de la série 4xxx (fils pour soudage) sont aptes à mûrir (durcissement structural).
Ce durcissement est dû à la formation, par germination et croissance (phénomène de démixtion = plusieurs phases non miscibles sont alors en présence, le temps détruisant peu à peu l'équilibre métastable généré par la trempe) des regroupements d'atomes initiés lors de la trempe, et qui ont pour effet de déformer localement le réseau cristallin.
Or, en métallurgie, chaque fois que l'on déforme la structure cristalline par formation de précipités comme ici, ou par écrouissage (=> formation de dislocations), on « durcit »...
Ces zones de regroupement d'atomes sont appelées zones de Guinier-Preston (voir article
« Aluminiums_Durcissement par précipitation.pdf », §2.3, p.3).
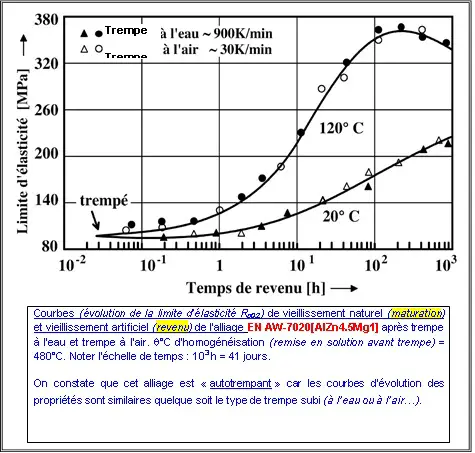
On parle de vieillissement artificiel (plus court - en temps - que le vieillissement naturel, voir courbes jointes) lorsque la pièce est durcie en étant chauffée entre 150 et 200°C pendant 5 à 25 h (voir article « Aluminiums_ Durcissement par précipitation.pdf », §2.3 p.4).
Ce vieillissement est appelé « revenu » et l'alliage est alors dit « trempé - revenu ». C'est l'état métallurgique T6. De la même manière, seuls les alliages des séries 2xxx, 6xxx et 7xxx (ainsi que quelques 4xxx : 4006[AlSiFe], 4007[AlSi1,5Mn], 4043A[AlSi5] (fil pour soudage), 4045[AlSi10] (fil pour soudage), 4046[AlSi10Mg] (fil pour soudage), 4047A[AlSi12] (fil pour soudage)) sont aptes à être durcis par un revenu (donc par « durcissement structural »).
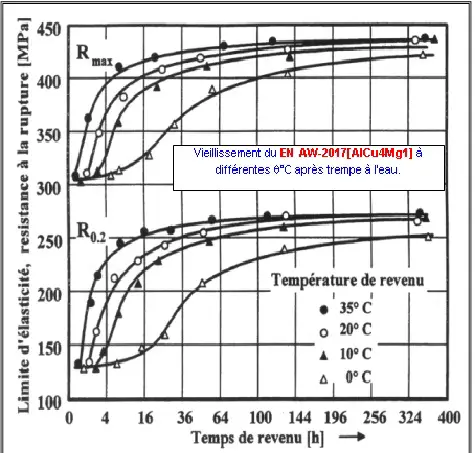
Métallurgiquement, ce revenu a pour effet de favoriser, comme précédemment mais plus rapidement (T°C plus élevée => mobilité plus grande des atomes) la création d'une multitude de petits précipités « d'AlSiMg » - lesquels sont dits « cohérents » (voir article « Aluminiums_Durcissement par précipitation. pdf », tableau 1 p.1) car ils déforment (= contraignent) localement très fortement le réseau cristallin, et « durcissent » d'autant plus la matrice qu'ils sont petits et nombreux (blocage maximal des déplacements des atomes au sein de la matrice contrainte).
Noter qu'une T°C plus élevée (recuit de « restauration » entre 250 et 300°C pendant 2 à 8h) aurait pour effet de créer des précipités plus gros et beaucoup moins nombreux - dits « semi-cohérents » ou « incohérents » - qui auraient un effet inverse à celui recherché (= ne déformant pas le réseau cristallin) et provoqueraient « l'adoucissement » du métal (chute des caractéristiques R[SUB]m[/SUB] et R[SUB]p0,2[/SUB] entre autres).
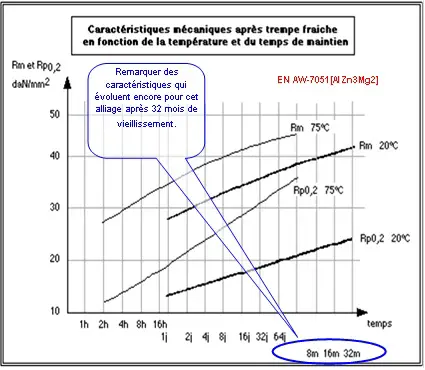
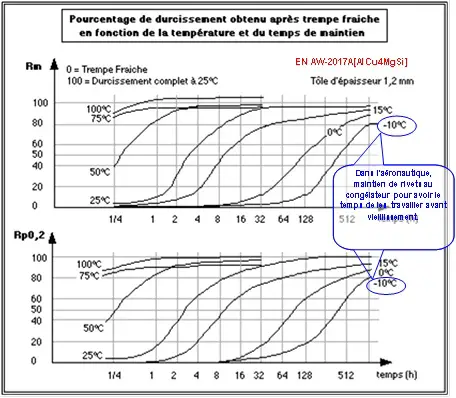
La norme ISO 15614-2 (§7.4.2 tableau 2, extrait ci-dessous) donne les coefficients d'efficacité T d'un joint soudé bout à bout.

On note que ceux-ci sont légèrement plus élevés pour la série 7xxx que pour la série 6xxx.
On note également que :
[SUP](e)[/SUP] « lorsque les assemblages de qualification sont vieillis artificiellement après soudage et avant essai (destructif), T s'applique à l'état T6 du matériau de base (avant soudage) », et donc non à l'état T4 comme mentionné dans le tableau, de telle sorte que, malgré des coefficients T apparemment égaux (0.7 pour la série 6xxx), les propriétés mécaniques du joint vieilli artificiellement sont supérieures à celles du joint vieilli naturellement.
C'est un peu différent pour la série 7xxx puisque les coefficients sont de 0.95 (naturel) et 0.75 (artificiel), de telle sorte que les propriétés mécaniques obtenues après maturation et revenu seront certainement très proches.
Dans le cas du soudage qui nous intéresse, la chaleur de l'arc provoque la modification de la structure de l'alliage dans la ZAT. Plusieurs phénomènes métallurgiques différents - étroitement dépendant de la T°C atteinte dans cette zone lors du soudage - peuvent être observés :
- Dans la zone la plus proche du cordon (zone « sous cordon », T°C la plus élevée ~ 500 à 550°C), se produit une remise en solution complète des précipités impliquant un adoucissement maximal et donc les propriétés mécaniques (R[SUB]m [/SUB], R[SUB]p0.2[/SUB] , H ,...) les plus faibles... Cette zone pourra évoluer dans le temps car la mise en solution a été faite, la matrice est sursaturée en éléments d'alliages (= elle contient les éléments d'alliages, Si, Zn, Mg, Cu, en solution, c'est-à-dire mélangés aux atomes d'Al mais sans plus aucun précipité, ceux-ci ont été dissous (= remis en solution) par la T°C. On dit « sursaturé », parce qu'à la T°C[SUB]ambiante[/SUB] , la matrice d'aluminium ne peut pas contenir autant d'atomes étrangers : cette « surabondance » d'atomes étrangers est le résultat de la trempe => équilibre métastable, voir diagrammes d'équilibres (= de phases)).
La matrice deviendra état T4 (elle « mûrira ») si on laisse le métal à la T°C[SUB]ambiante[/SUB].
- Dans les deux zones suivantes, un peu plus loin du cordon (T°C ~ 350 à 400°C, q°C ~ 160 à 350°C), se produit un recuit dit « de coalescence - ou précipitation » se traduisant par une transformation des petits précipités, nombreux (mentionnés précédemment) en de plus gros beaucoup moins nombreux (c'est le phénomène de coalescence), et surtout incohérents (= ne déformant pas, ne contraignant pas la matrice ; ne bloquant plus le déplacement des atomes) avec la matrice (leur grosseur (et leur nombre) dépend de la T°C et du temps de maintien à cette T°C ; dans la zone T°C ~ 160 à 350°C, on parle de « sur-revenu » = état T7).
Ces (gros) précipités, dès lors, ne constituent plus d'obstacles aussi infranchissables que (les petits précipités) précédemment (voir T.Ingénieur « M1290_Traitements thermiques des alliages d'aluminium.pdf », pages 10 et 15) pour les atomes et donc ne « durcissent » plus...
Cette faculté redonnée aux atomes, par l'apport de chaleur de l'arc, de se déplacer librement, détruit donc les effets du Traitement thermique initial - T6 ici - et provoque une chute des caractéristiques mécaniques jusqu'à une valeur de 60% (soit T = 0,6) de la résistance à la rupture R[SUB]m[/SUB] initiale, on parle d'« adoucissement ». On peut estimer, dans des proportions identiques, une chute de la limite élastique R[SUB]e[/SUB] (ou R[SUB]p0,2[/SUB] dans le cas des aluminiums), (voir les courbes et la norme ISO 15614-2).
Et cette situation ne pourra plus évoluer positivement car la matrice n'est plus sursaturée (= les éléments d'alliages ayant précipité en gros précipités incohérents, il n'y en a plus, ou presque, en solution - c'est-à-dire mélangés aux atomes d'Al sans aucun précipité - dans la matrice d'aluminium, alors quasiment pure et devenue « molle » comme tout matériau métallique pur) sauf si on retrempe à nouveau tout l'ensemble (remise en solution (des gros précipités) suivie d'une trempe).
C'est la 3[SUP]ème[/SUP] raison (mentionnée précédemment) pour opérer avec une vitesse de soudage relativement rapide (le temps étant, bien entendu, un paramètre important dans toute opération de soudage) limitant au maximum le séjour du métal à haute température (et corollairement l'apport de chaleur) : les énergies de soudage doivent être les plus faibles possibles (avec un temps court : W = U x I x t ; et une zone chauffée faible => P = U x I est importante lorsque la surface chauffée est faible ; le procédé de soudage par LASER, par exemple, réalise très bien ces conditions de soudage) pour limiter la coalescence des précipités, le sur-revenu et l'adoucissement de la ZAT, et corollairement, les cordons de soudures les plus limités possibles en longueur.
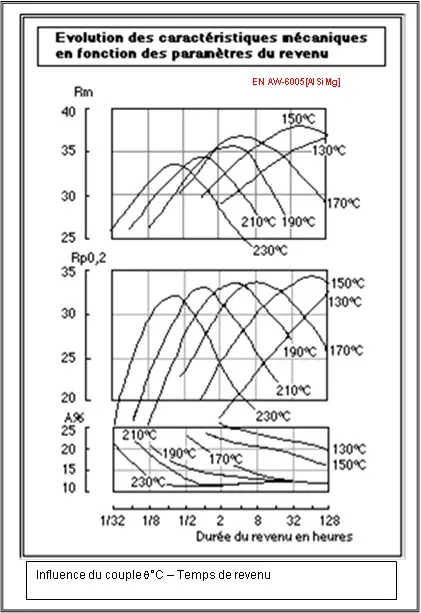
La seule façon de faire pour que les pièces retrouvent une grande partie (voir norme ISO 15614-2 sur les valeurs des coefficients T) de leurs caractéristiques mécaniques initiales est de réaliser une mise en solution complète de toute la pièce suivie d'une trempe puis d'un revenu à T°C ~ 160°C préconisé pendant ~ 20h (vieillissement artificiel - état T6 - voir courbes ci-dessus).
De plus, ce revenu à ~ 160°C pourra, dans une certaine mesure, servir à détensionner partiellement, la pièce soudée, en vue des usinages ultérieurs (l'idéal aurait été de détensionner à T°C ~ 250°C pendant 8h suivi d'un refroidissement lent mais cela conduirait à effectuer un sur-revenu (état T7) et donc à re-perdre l'essentiel des caractéristiques mécaniques, tout le dilemme est là).
Noter que :
- Le vieillissement naturel (état T4) permet de « remonter » les caractéristiques mécaniques mais dans des proportions moins importantes que le vieillissement artificiel.
- La résistance du joint soudé en série 6xxx est toujours inférieure à celle du métal de base (les coefficients d'efficacité T des joints - rapport entre la R[SUB]m[/SUB] après soudage et la R[SUB]m[/SUB] avant soudage - ont du mal à dépasser les 75%..., voir norme ISO 15614-2).
3 - Données métallurgiques sur le métal d'apport :
Dans l'article joint « Soudage TIG et MIG de l'Aluminium et ses alliages_Pratique du soudage.doc », il est indiqué au §18 : « Le métal d'apport utilisé doit être de même composition et de même degré de pureté que le métal de base à souder », ce que ne semble pas corroborer ce même article ni l'article des T.Ingénieur
« M439_Propriétés technologiques de l'aluminium et ses alliages corroyés.pdf », tableau 4, page 7, qui par contre, se rejoignent sur les nuances à utiliser, c'est déjà ça...
Les Métaux d'apport recommandés pour la série 6xxx sont les suivants :
- La série 5356 (AlMg5) (les séries 5183, 5356 et 5556 sont sensibles à la corrosion sous contrainte mais je ne sais pas pourquoi...).
- S'il n'y a pas d'anodisation ultérieure, la série 4043 (nuance à durcissement structural => qui peut vieillir) est utilisable, sinon non (car gris foncé très mat après anodisation).
- Pour des pièces travaillant à la chaleur (100°C à 200°C), les séries 4043 ou 4047(AW[AlSi12]) (nuances qui peuvent vieillir).
- Pour des pièces qui subissent un traitement thermique après soudage, la série 4643 (d'après le Catalogue ESAB, p.7 : le 4643 est un alliage qu'il est possible de traiter thermiquement et qui peut donc vieillir. Il présente de meilleures résistances dans les ensembles soudés de la série 6xxx lorsque des solutions de traitement thermique ou de vieillissement après soudage sont appliquées). Celui-ci semble permettre d'obtenir 90% de la R[SUB]m[/SUB] du métal de base (donc T = 0,9, ça vaudrait le coup de vérifier !!...). Le 4643 (AW[AlSi4]) est donné comme similaire au 4043 (AW[AlSi5]).
J'ai par ailleurs relevé :
- Dans les T.Ingénieur « M439_Propriétés technologiques de l'aluminium et ses alliages corroyés.pdf » p.6, §2.1.3 : « Alliages de la série 6xxx (Al-Mg-Si) : très bonne soudabilité opératoire à condition d'utiliser un métal d'apport du type Al-Si (4043) ou Al-Mg (5356) (sans métal d'apport, ces alliages sont très sensibles à la fissuration mais je ne sais pas pourquoi...). Soudés sur état revenu (T5 ou T6) le coefficient d'efficacité du joint T varie entre 0,45 et 0,6 ». (un peu plus faible que dans la norme ISO 15614-2, et beaucoup plus faible que dans le catalogue ESAB).
« Alliages de la série 7xxx sans Cu (Al-Zn-Mg) (alliage représentatif 7020) : soudabilité opératoire moins favorable que celle des alliages de la série 6xxx mais acceptable à condition d'utiliser un métal d'apport chargé en magnésium (5356 ou 5183). Du fait de sa faible vitesse critique de trempe (alliage autotrempant), l'alliage durcit par maturation après soudage et le coefficient de joint T est de l'ordre de 0,8 un mois après soudage (donc similaire à norme ISO 15614-2). Par contre, la ZAT est plus sensible à certains phénomènes de corrosion et l'utilisation du 7020 en construction soudée nécessite des protections contre l'environnement. »
- Dans les T.Ingénieur « M440_Propriétés de l'aluminium et des alliages d'aluminium corroyés.pdf » :
- p.6, §1.4.1.1 : « L'alliage 4043 à 5 % environ de silicium est recommandé toutes les fois que les alliages à souder ou les types d'assemblages à réaliser présentent des difficultés du point de vue soudabilité opératoire (risque de fissuration (à chaud certainement) en particulier). » « L'alliage 4043 est, de plus, en pratique systématiquement conseillé dans le cas du soudage des alliages d'aluminium de moulage ainsi que dans le cas du soudage d'un alliage d'aluminium de moulage avec un alliage d'aluminium de transformation (corroyé)... ».
- p.8, §1.5.3 : « Alliages pour métal d'apport en soudage : en raison de leur bonne soudabilité opératoire, les alliages Al-Mg sont très utilisés en tant que métal d'apport lors du soudage des différents alliages d'aluminium. Différentes nuances d'alliages ont été spécialement mises au point à cet égard, tant du point de vue composition (présence de titane pour affiner le grain de la zone fondue, de béryllium pour limiter l'oxydation) que du point de vue fabrication du fil lui-même (états de surface spéciaux). Les alliages les plus utilisés sont les nuances (voir T.Ingénieur
« M438_Aluminium et alliages d'aluminium corroyés : propriétés métalliques.pdf ») :
[*]5554, 5654, 5754, 5854 ;
[*]5183 ;
[*]5356, 5556. »
Une hypothèse toute personnelle pouvant donner une raison supplémentaire de l'utilisation des alliages de la série 5xxx comme métal d'apport est la « souplesse » générale à chaud (ductilité) de ces alliages, par ailleurs recommandés pour le filage à chaud, souplesse pouvant permettre d'éviter les phénomènes de fissuration à chaud que ne permettrait peut-être pas un métal d'apport de même nuance que celle du métal de base, surtout dans la série 7xxx, qui pose beaucoup plus de problèmes de soudabilité.
4 - Informations complémentaires :
J'ai par ailleurs relevé :
- Dans les T.Ingénieur « B7730_Soudage à l'arc.pdf » p.16, §4.3 : « Le soudage MIG est la solution semi-automatique et automatique des assemblages en alliages d'aluminium et en aciers inoxydables dans la chaudronnerie des réservoirs transportés, des silos propres et des conteneurs des industries agro-alimentaires.
Malgré les tentatives faites dans la composition des fils et des gaz, très vite limitée en comparaison avec les flux ou les enrobages, les soudures MIG/MAG ne sont pas performantes du point de vue mécanique (manque de compacité) et métallurgique (appauvrissement des liaisons en éléments d'apport). Le procédé n'est donc pas pris en considération dans les cas critiques. »
- Dans les T.Ingénieur « M715_Soudage et soudabilité métallurgique des métaux.pdf » p.22, 23 et 24, §6.1 au sujet des alliages d'aluminium : « Sa conductivité thermique élevée impose la mise en œuvre de sources de chaleur à grande densité d'énergie afin de permettre une réduction de la durée des cycles thermiques de soudage et cela malgré la basse température de fusion du métal de base (il peut être nécessaire de procéder à un préchauffage pour limiter la quantité d'énergie à mettre en œuvre... NDLR : à une T°C inférieure à la T°C du revenu T6 pour ne pas adoucir...). Le niveau de cette conductivité a une contrepartie favorable en ce sens qu'il induit une diminution des gradients thermiques et, de ce fait, conduit à des déformations moins localisées. »
« Son module d'élasticité relativement faible limite favorablement l'amplitude des contraintes résiduelles. »
« Ainsi donc le soudeur devra, pour souder des alliages d'aluminium, mettre en œuvre des procédés à grande densité d'énergie et permettant de protéger efficacement le métal contre l'action de l'oxygène. »
« Si le métal de base est un alliage durci par traitement thermique (alliages des séries 2xxx, 6xxx et 7xxx, voire 4xxx), le soudage peut engendrer un adoucissement, par sur-revenu d'une part, et par remise en solution des précipités d'autre part. Dans ce dernier cas seulement, il peut être envisagé de provoquer un re-durcissement à l'aide d'un nouveau revenu ou, si l'alliage le permet, par maturation à la T°C[SUB]ambiante[/SUB]. D'une manière générale, il subsiste toujours (si les conditions pratiques le permettent), la possibilité de reprendre dans son intégralité le traitement thermique après soudage. »
5 - Conclusion générale :
Le 7020 semble être l'alliage susceptible de présenter les caractéristiques mécaniques les plus élevées après soudage (voir coefficients T de la norme ISO 15614-2) et vieillissement artificiel, mais il pose beaucoup plus de problèmes que le 6082 en termes de soudabilité et de sensibilité à l'environnement lors du soudage (corrosion).
Quoiqu'il en soit du choix (6082 ou 7020),
la gamme qui me semble la plus adaptée compte-tenu du Cdcf donné est la suivante :
- Soudage MIG (avec paramètres précédemment définis : U, I, gaz de protection, vitesse de soudage, mode de transfert du fil, métal d'apport,... => perte du traitement T6) en soudant le plus loin possible des usinages à effectuer, le plus symétriquement possible par rapport à ceux-ci avec des cordons courts ;
- Usinage ébauche ;
- Mise en solution et trempe, puis revenu à T°C ~ 160 à 190°C pendant quelques heures (voir courbes du métal concerné), pouvant laisser espérer un léger détensionnement (ceci dit, voir le § « Informations complémentaires - M715 », plutôt favorable au sujet des déformations) ;
- Usinage finition.
avec de grandes « chances » de ne pas retrouver après tout ça notre limite conventionnelle d'élasticité (Cdcf)
R[SUB]p0,2[/SUB] ≥ 200 MPa
Seuls des essais de soudage et des essais mécaniques permettraient de valider le choix et modifier éventuellement le CdCf.
Une solution qui pourrait permettre de s'affranchir d'une gamme aussi compliquée serait d'envisager de souder par LASER : l'avantage de ce procédé de soudage est de quasiment supprimer la ZAT du fait de la possibilité donnée par le Laser, de fusion très rapide et très localisé du métal de base.
Plus de ZAT =>
- Plus de remise en solution et d'adoucissement => pas de perte du traitement T6 => conservation des caractéristiques mécaniques initiales ;
- Plus de déformation sur les pièces.
Une solution intermédiaire pourrait être le « soudage LASER hybride » :
dérivé du soudage laser, il combine le soudage laser avec la technique du soudage MIG (entre autres). Cette combinaison permet une grande souplesse de positionnement des pièces car le MIG apporte du métal en fusion pour remplir le joint, et l'usage du laser augmente la vitesse de travail par rapport à ce qui est possible avec le système à arc seul. La qualité du soudage en est grandement améliorée...
Reste plus quà se renseigner sur les coûts de ces procédés de soudage... Vous les trouverez très certainement sur ce site...
6 - Vos questions en relation avec cet article sur le forum du site
Vous avez la possibilité de poser vos différentes questions sur le forum technique de ce site.
Le lien du forum est le suivant :

7 - Quelques liens Internet utiles










8 - Vos commentaires et réactions sur cet article
Envoyer un message privé à l'auteur Gérard Lignier :

Vous avez la possibilité de commenter cette page, de réagir ou de compléter les informations en rédigeant un message dans le cadre ci-dessous intitulé Ecrire un commentaire.
Vos commentaires seront visibles aux lecteurs de l'article et membres du site.
Vous avez aussi la possibilité de noter l'article avec le système de notation par nombre d'étoiles placé en début de page de chaque article.
Nous vous remercions par avance de votre sollicitude et de votre aide pour l'amélioration des données techniques du site.
Nous rappelons à nos aimables visiteurs que nos ressources techniques et nos croquis ne peuvent être ni copiés ni utilisés sans autorisation écrite de notre part.
9 - Un petit geste pour soutenir votre site web spécialisé technique soudage



Par: Gérard Lignier